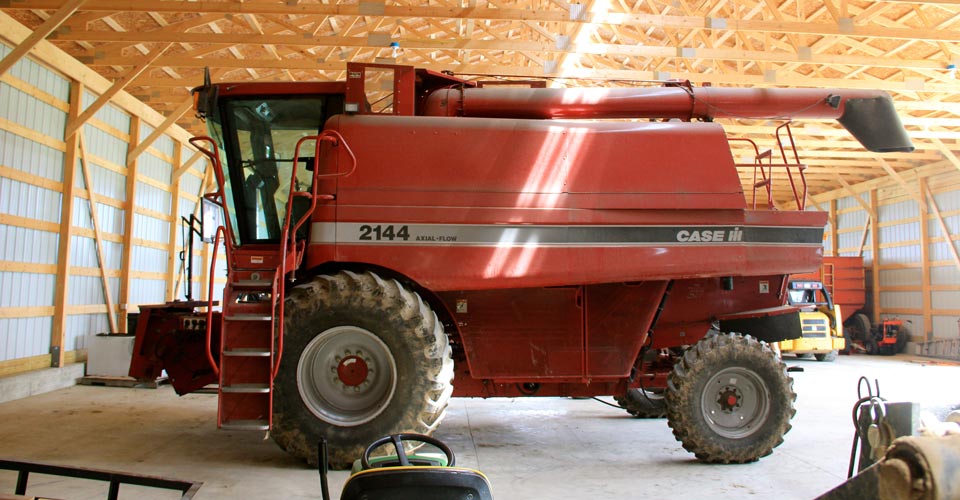
By Jon Woetzel, Manager Technical Services, Energy Lubricants, CHS from the Cenexperts blog
Harvest is tough. Once you’ve made it through some of the hardest weeks of the year, both you and your equipment deserve some R&R. But before your machines take a long winter’s nap, it’s important to get them ready for sitting dormant in the cold.
Even when your equipment isn’t running, lubricants play an essential role in keeping it protected. That’s why, as part of your yearly winterizing routine, you’ll want to assess your equipment’s fluids. Use these four lubricant tasks to protect your rigs all the way to spring.
1. Get a used oil analysis
Throughout harvest, your machines work overtime to meet the grueling demands of a farm’s busiest time of year. By the end of the season, all that wear and tear can take a toll on an engine, and seemingly small issues at this point can lead to bigger problems come spring.
A used oil analysis is an easy way to catch early warning signs of major issues that could be brewing inside your engine. This is because oil is the lifeblood of your equipment, touching nearly every part inside the engine.
Used oil analysis works by detecting any trace elements present in a sample of used oil from inside your rig. Based on the elements that turn up, lab technicians can identify a number of issues that may be waiting to happen in specific areas of your engine. Fix any issues before putting your equipment away, and you’ll set yourself up for success come time for planting. To get started, you can purchase a used oil analysis kit from your local CHS energy specialist.
2. Replace the engine oil
Once you’ve performed a used oil analysis, you may also want to consider an oil change before you put your machines away for winter. This is especially true if the results of your analysis reveal any traces of wear. After you make any repairs recommended by your analysis, give your machines some fresh, clean oil so you don’t leave acids and contaminants festering inside your engine for months on end.
Even if your used oil analysis comes back clean, you may still want to consider replacing your oil before winter. Remember, the longer an oil has been used, the less effective it becomes at protecting against rust and corrosion.
If you’re getting close to your change interval, it’s best to replace oil this season instead of waiting until spring. Just be sure to run the engine for at least 10 minutes before storing your rig to allow the oil to circulate. For protection all winter long, try a high-quality engine oil from Cenex such as MAXTRON® ENVIRO-EDGE® synthetic diesel engine oil, engineered for maximum lifespan and excellent protection against corrosive wear.
3. Top off your hydraulic tank
Another lubricant tip for winterizing your equipment is to top off hydraulic tanks. To function properly, hydraulic systems need to breathe, but since they’re not airtight, they’re prone to letting in moisture as equipment sits all winter. Condensation inside a hydraulic system is bad news due to the harmful corrosion it may cause.
The best way to prevent condensation in your hydraulic system over the winter is to minimize the airspace inside. The less opportunity air has to get in, the lower the chance that moisture will collect. Check your hydraulic fluid level, and if it’s not full, go ahead and top off your tank. Be careful, though, not to overfill. To further minimize condensation, you may also want to consider switching to a hydraulic fluid designed to prolong the life of your system’s seals, like MAXTRON® THF+.
4. Grease up moving parts
Finally, once you’ve taken care of your machines’ other fluids, complete the job by greasing any moving parts. Even though they’ll be sitting still all winter, moving parts can still corrode.Not only will a fresh coat of grease keep your equipment from rusting through the winter but it will also get it moving again easier come spring. For superior protection against rust and corrosion, try a Cenex grease such as MAXTRON® FS.
When the hard work of harvest is over, it can be tempting to overlook details like winterizing your equipment. But the period right after harvest is a valuable opportunity to take care of maintenance tasks that can fall through the cracks during busier times of year. Give your machines some TLC now, and you can both kick back soon for some well-deserved hibernation.